Intercambiadores de calor en aplicaciones industriales
Los intercambiadores de calor son fundamentales para transferir energía térmica entre fluidos. Este proceso desempeña un papel importante en las industrias que requieren control de temperatura para lograr eficiencia y seguridad operativas. Las aplicaciones típicas incluyen:
Industria química: se utilizan en procesos como la destilación, la condensación y el enfriamiento de reacciones. Los intercambiadores de calor ayudan a mantener temperaturas específicas para controlar las velocidades de reacción y garantizar la consistencia del producto.
Industria petrolera: Esencial para los procesos de refinación, donde el crudo pasa por fases de calentamiento y enfriamiento. Los intercambiadores ayudan en el craqueo, la destilación y la separación de productos.
Generación de energía: En las centrales térmicas se utilizan intercambiadores de calor para condensar el vapor y reutilizarlo en la caldera, optimizando la eficiencia del combustible.
Procesamiento de Alimentos: Los intercambiadores ayudan en los procesos de pasteurización y esterilización, manteniendo la calidad y seguridad de los productos alimenticios.
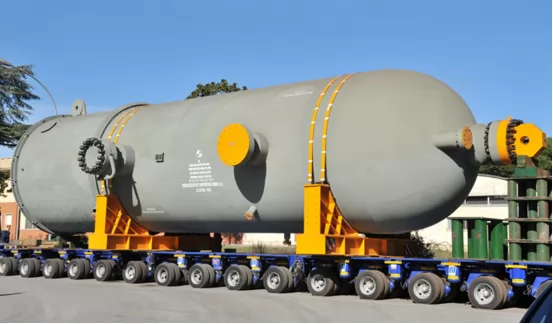
Clasificación de los intercambiadores de calor:
- Tipo de partición: utiliza una pared sólida para separar los fluidos. Entre los ejemplos se incluyen los intercambiadores de calor de carcasa y tubos y de placas, ampliamente utilizados por su alta eficiencia y facilidad de mantenimiento.
- Tipo híbrido: permite la mezcla parcial de fluidos, adecuado para aplicaciones donde una mezcla controlada de fluidos es beneficiosa.
- Tipo de almacenamiento de calor: almacena calor temporalmente en un medio antes de transferirlo a otro fluido. Se utilizan en aplicaciones que requieren calentamiento cíclico o intermitente.
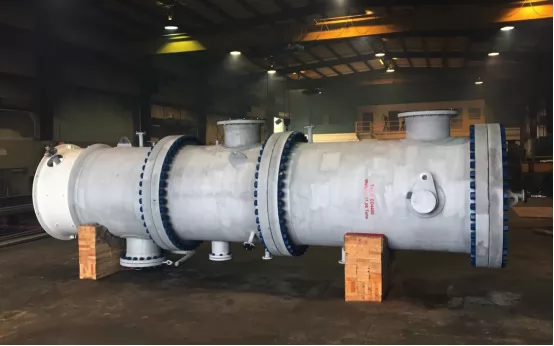
Selección de materiales para intercambiadores de calor
Metales: La elección del material depende de las presiones de operación, las temperaturas y la corrosividad del fluido:
- Acero al carbono: Económico y adecuado para temperaturas bajas a moderadas. Se utiliza habitualmente en intercambiadores de agua a agua.
- Acero inoxidable: resistente a la corrosión, lo que lo hace adecuado para entornos de alta temperatura y alta presión. Se utiliza ampliamente en las industrias química, alimentaria y farmacéutica por su falta de reactividad y facilidad de limpieza.
- Níquel y aleaciones de níquel: Alta resistencia a la corrosión y oxidación a temperaturas extremas, comúnmente utilizados en procesos petroquímicos e intercambiadores de alta presión.
- Titanio: conocido por su excepcional resistencia a la corrosión, a menudo se utiliza en aplicaciones de agua de mar o salmuera debido a su durabilidad y propiedades no corrosivas en entornos de agua salada.
- Materiales no metálicos: Ciertas aplicaciones implican intercambiadores de calor no metálicos, especialmente en entornos altamente corrosivos:
- Intercambiadores de cerámica: ideales para temperaturas extremas y productos químicos corrosivos, pero generalmente más costosos y menos adaptables a altas presiones.
- Polímeros: Ligeros y muy resistentes a la corrosión, sin embargo su uso está limitado a temperaturas y presiones más bajas.
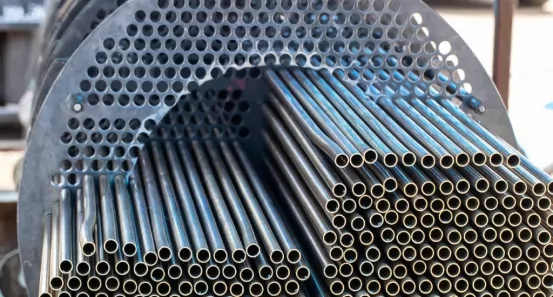
Corrosión del intercambiador de calor y estrategias de mantenimiento
- Preocupaciones por la corrosión: la transferencia de calor acelera la corrosión, especialmente en condiciones de ebullición o vaporización. La velocidad de corrosión también depende del medio fluido (por ejemplo, salino, ácido).
- Técnicas de prevención de la corrosión:
- Recubrimientos de materiales: la aplicación de recubrimientos como epoxi o el uso de materiales de revestimiento pueden prolongar la vida útil del equipo.
- Inhibidores de corrosión: adición de productos químicos específicos a los fluidos para reducir las interacciones corrosivas.
- Protección electroquímica: métodos como la protección catódica pueden reducir la corrosión en entornos agresivos.
- Protocolos de mantenimiento: Las inspecciones y limpiezas programadas son esenciales para evitar la acumulación de residuos, que puede provocar bloqueos, pérdida de eficiencia y mayor desgaste.
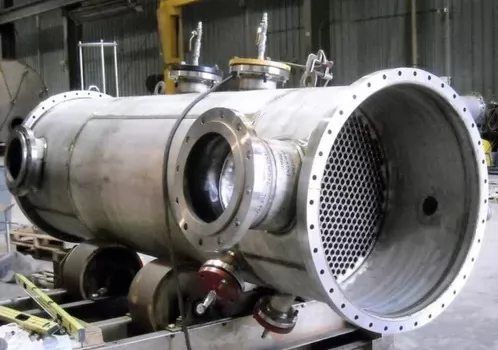
Procesos de soldadura y el papel de los rotadores de soldadura
- Importancia de la soldadura en la fabricación de intercambiadores de calor: la soldadura precisa garantiza la integridad estructural bajo alta presión y estrés térmico. Se seleccionan diferentes tipos de soldadura (por ejemplo, TIG, MIG y soldadura por arco sumergido) en función de los requisitos de diseño y material.
- Uso de rotadores de soldadura:
- Estabilidad mejorada: Los rotadores estabilizan los componentes cilíndricos, garantizando soldaduras uniformes y consistentes.
- Mano de obra manual reducida: la rotación automatizada minimiza los ajustes manuales, mejorando la productividad y la precisión de la soldadura.
- Protección de la superficie: Los rodillos de poliuretano en los rotadores protegen contra rayones y mantienen la calidad de la superficie, algo especialmente crucial cuando se manipulan materiales pulidos o sensibles.
- Versatilidad: Los rotadores pueden manejar distintos tamaños y formas, lo que admite la producción de múltiples procesos (soldadura, arenado, pintura).
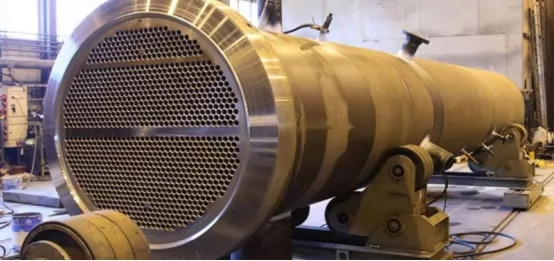
Aplicaciones especializadas de los intercambiadores de calor
- Aeroespacial: Los intercambiadores de calor son esenciales para la regulación de la temperatura en los sistemas de combustible y los controles ambientales dentro de las aeronaves.
- Semiconductores: fundamentales en la fabricación de productos electrónicos, donde se necesita un enfriamiento preciso para los procesos de producción y ensamblaje de chips.
- Turbinas eólicas: Los enfriadores de aceite en las cajas de engranajes de las turbinas eólicas garantizan un funcionamiento eficiente.
- Plantas de energía solar: se utilizan en sistemas de almacenamiento térmico para transferir la energía solar recolectada durante el día para su uso durante las horas no soleadas.
- Equipos de atención médica: en dispositivos médicos como las máquinas de resonancia magnética, los intercambiadores ayudan a mantener la estabilidad de la temperatura para lograr la precisión operativa y la seguridad del paciente.
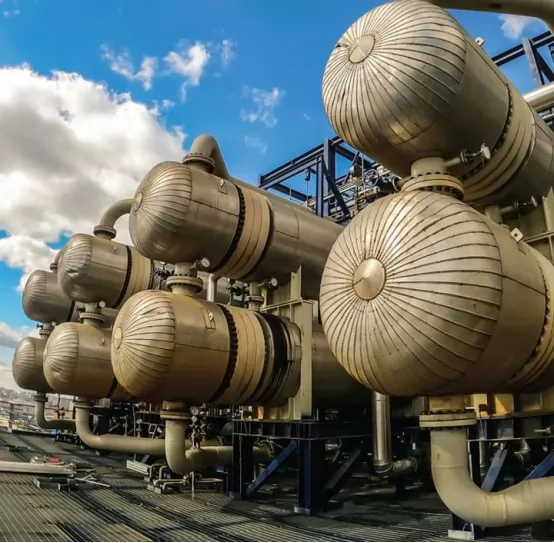
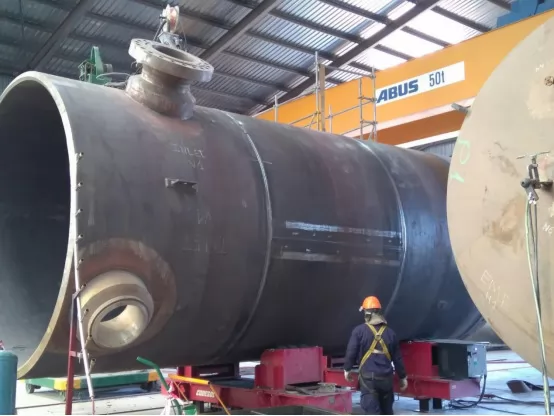
Proceso de fabricación de intercambiadores de calor
- Preparación del material: Esto incluye la selección y verificación de los grados de metal, que luego se inspeccionan para detectar defectos.
- Conformado y ensamblaje: incluye procesos como el laminado y la soldadura, donde los rotadores de soldadura juegan un papel clave.
- Pruebas y garantía de calidad:
- Prueba de presión: garantiza que el intercambiador pueda soportar presiones de operación sin fugas.
- Pruebas no destructivas (NDT): técnicas como las pruebas ultrasónicas y las inspecciones con rayos X detectan fallas internas sin dañar el producto.
- Ensamblaje final y revestimiento: para aplicaciones específicas, se puede aplicar un revestimiento o acabado protector para garantizar la longevidad.
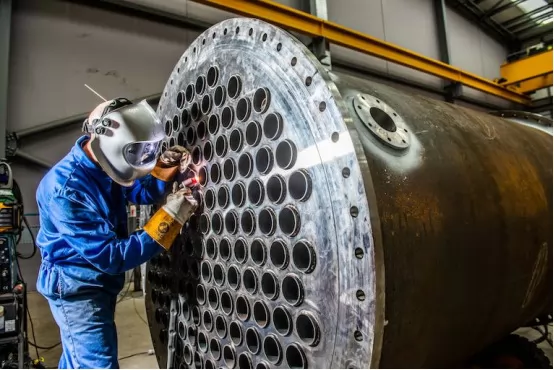
Ventajas y desafíos del uso de intercambiadores de calor
Ventajas:
- Eficiencia energética: La recuperación de calor mediante intercambiadores reduce el consumo de combustible y energía.
- Optimización de procesos: facilita el control de la temperatura, lo cual es fundamental para mantener la calidad del producto y la estabilidad del proceso.
- Beneficios ambientales: Un menor consumo de energía contribuye directamente a reducir las emisiones de gases de efecto invernadero.
Desafíos:
- Corrosión e incrustaciones: frecuentes en entornos de alta temperatura y alta presión, la corrosión y la acumulación de residuos requieren un mantenimiento regular y soluciones de diseño innovadoras.
- Fabricación compleja: la precisión requerida para una soldadura de alta calidad y la compatibilidad de los materiales hacen que la fabricación sea laboriosa y tecnológicamente exigente.
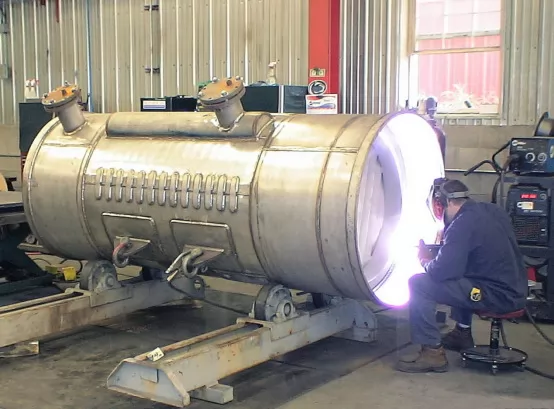
8. Tendencias futuras en la tecnología de intercambiadores de calor
- Materiales avanzados: Desarrollo de materiales compuestos que proporcionen resistencia a la corrosión y conductividad térmica superiores.
- Miniaturización: Especialmente en electrónica y sanidad se necesitan intercambiadores más pequeños y altamente eficientes.
- Fabricación aditiva (impresión 3D): permite geometrías complejas y diseños de intercambiadores de calor personalizados que antes eran imposibles con los métodos tradicionales.
- Monitoreo inteligente: Integración de sensores IoT para monitorear el rendimiento y predecir las necesidades de mantenimiento, reduciendo el tiempo de inactividad y mejorando la eficiencia.
Aplicación de equipos de soldadura y posicionamiento en la producción de intercambiadores de calor
En la fabricación de intercambiadores de calor, los equipos de soldadura y posicionamiento son fundamentales para lograr una alta precisión y cumplir con los exigentes requisitos estructurales. A continuación, se muestra cómo contribuyen al proceso los distintos tipos de equipos:
1. Rotadores de soldadura:
- Función: Los rotadores de soldadura proporcionan una rotación estable y controlada para componentes cilíndricos, como carcasas y haces de tubos, lo que permite a los soldadores aplicar soldaduras uniformes. Al sostener la pieza de trabajo, los rotadores reducen la manipulación manual, aumentan la productividad y garantizan una calidad constante.
Beneficios:
- Protección de la superficie: Los rodillos de poliuretano evitan que se raye la superficie del cilindro.
- Soldadura eficiente: La rotación controlada permite una soldadura continua, minimizando la necesidad de soldaduras de inicio y parada, que pueden introducir puntos débiles.
- Aplicaciones: Además de la soldadura, los rotadores también son valiosos en procesos como el arenado, la limpieza y la pintura.
2. Posicionadores:
- Función: Los posicionadores mantienen los componentes del intercambiador de calor en su lugar, lo que permite una orientación precisa durante la soldadura. Son especialmente útiles para componentes grandes o de forma irregular que son difíciles de girar o mover manualmente.
Beneficios:
- Acceso mejorado: los posicionadores permiten a los soldadores acceder a áreas difíciles de alcanzar, lo que garantiza una cobertura completa y reduce la posibilidad de uniones débiles.
- Versatilidad: Los posicionadores se pueden ajustar para distintos ángulos, lo que resulta beneficioso en conjuntos complejos como intercambiadores de tubos en U y multitubos.
- Aplicaciones: Los posicionadores se utilizan comúnmente durante el ensamblaje y la soldadura de haces de tubos, placas de tubos y juntas de carcasa.
3. Manipuladores de soldadura:
- Función: Los manipuladores de soldadura proporcionan un soporte estable y ajustable para las antorchas de soldadura, lo que garantiza soldaduras precisas y estables. Estos se pueden ajustar de forma manual o automática para adaptarse a la configuración del intercambiador de calor.
•Beneficios:
- Precisión: Los manipuladores ayudan a mantener una distancia constante entre el arco de soldadura y la pieza de trabajo, lo cual es crucial para lograr soldaduras uniformes y de alta calidad.
- Seguridad: Reducen la fatiga del operador al apoyar la herramienta de soldadura, lo que permite que los operadores se concentren en controlar el proceso de soldadura.
- Aplicaciones: Los manipuladores se utilizan a menudo en soldaduras de costura larga, especialmente en intercambiadores de calor de carcasa y tubos grandes donde la alineación precisa de la soldadura es fundamental.
4. Accesorios y abrazaderas para soldadura:
- Función: Los accesorios y abrazaderas son esenciales para mantener los componentes firmemente en su lugar durante la soldadura, garantizando que las piezas no se muevan bajo estrés térmico.
Beneficios:
- Precisión: evita la desalineación, que puede provocar soldaduras débiles y costosas repeticiones de trabajos.
- Consistencia: Estandariza el posicionamiento, especialmente útil para producción de gran volumen.
- Aplicaciones: Los accesorios y abrazaderas se utilizan en el ensamblaje de haces de tubos y componentes de carcasa, garantizando la estabilidad durante la soldadura.
Proceso detallado de soldadura para intercambiadores de calor
El proceso de soldadura en la producción de intercambiadores de calor implica varias técnicas especializadas, cada una seleccionada en función del material, la geometría del componente y los requisitos de diseño. A continuación, se ofrece una descripción paso a paso:
1. Etapa de preparación:
- Inspección y preparación de materiales: Todos los materiales se someten a una inspección para garantizar el cumplimiento de las especificaciones. La limpieza de la superficie es esencial para eliminar contaminantes como aceite, óxido y óxidos, que podrían debilitar la soldadura.
- Preparación de los bordes: cortar, biselar y preparar los bordes para soldar crea el ajuste y el ángulo adecuados para lograr uniones de soldadura resistentes. Para secciones gruesas, pueden ser necesarias soldaduras de varias capas, y una preparación adecuada de los bordes permite un control más fácil de cada capa.
2. Técnicas de soldadura habituales en la producción de intercambiadores de calor:
- Soldadura con gas inerte de tungsteno (TIG):
- Aplicación: La soldadura TIG se utiliza comúnmente para acero inoxidable y metales no ferrosos como aleaciones de níquel, proporcionando un control preciso y soldaduras de alta calidad.
- Ventajas: Ofrece soldaduras limpias con mínimas salpicaduras, lo que es crucial en aplicaciones donde la higiene (por ejemplo, intercambiadores de alimentos y productos farmacéuticos) y la resistencia a la contaminación son fundamentales.
- Soldadura de metal con gas inerte (MIG):
- Ventajas: Es más rápido que el TIG e ideal para soldaduras de costura larga, donde la velocidad y la eficiencia son prioridades.
- Aplicación: La soldadura MIG se utiliza a menudo para acero al carbono y es adecuada para soldadura de alta velocidad en conjuntos grandes.
- Soldadura por arco sumergido (SAW):
- Ventajas: Proporciona una penetración profunda y alta resistencia de soldadura, lo que lo hace adecuado para aplicaciones de alta presión.
- Aplicación: SAW es ideal para costuras largas y rectas en materiales más gruesos, como las carcasas de grandes intercambiadores de calor de carcasa y tubos.
- Soldadura por arco de plasma (PAW):
- Aplicación: Se utiliza en aplicaciones que requieren alta precisión, como la soldadura de placas de tubo a tubo, donde la consistencia y el control son esenciales.
- Ventajas: Proporciona un arco estrecho y enfocado, permitiendo soldaduras precisas y profundas, adecuado para trabajos finos y detallados.
3. Control de calidad e inspección de la soldadura:
- Inspección visual: controles iniciales para detectar defectos en la superficie, como grietas, porosidad y problemas de alineación.
- Pruebas no destructivas (END):
- Prueba ultrasónica (UT): utiliza ondas sonoras para detectar fallas internas sin dañar el componente.
- Pruebas radiográficas (RT): Las inspecciones con rayos X o rayos gamma revelan defectos ocultos, garantizando la integridad de la soldadura.
- Prueba de penetración de tinte (DPT): eficaz para detectar grietas superficiales, especialmente en materiales no magnéticos como el acero inoxidable.
- Prueba de presión: garantiza que el componente soldado pueda soportar las presiones de funcionamiento. Los métodos más comunes incluyen pruebas hidrostáticas, en las que el intercambiador se llena con agua y se presuriza para verificar si hay fugas.
4. Procesos post-soldadura:
- Tratamiento térmico: Ciertos materiales requieren un tratamiento térmico posterior a la soldadura (PWHT) para aliviar las tensiones residuales y mejorar la integridad estructural, especialmente en intercambiadores de alta presión.
- Acabado de superficies: incluye procesos como el arenado, el esmerilado y el pulido. En aplicaciones en las que la limpieza es esencial (por ejemplo, intercambiadores de alimentos), los acabados pulidos evitan el crecimiento bacteriano y la contaminación.
5. Sistemas de soldadura automatizados:
- En la fabricación moderna, se utilizan cada vez más sistemas de soldadura automatizados con brazos robóticos y controladores programables. Estos sistemas ofrecen un control preciso, repetibilidad y alta velocidad de producción, lo que resulta especialmente beneficioso para la producción a gran escala. La integración de la automatización con rotadores y posicionadores de soldadura maximiza la eficiencia y minimiza el error humano.
Aplicaciones avanzadas de equipos de soldadura en la producción especializada de intercambiadores de calor
1. Centrales nucleares:
- Los equipos de soldadura de alta especificación garantizan la confiabilidad de los intercambiadores de calor que operan en temperaturas y presiones extremas dentro de los reactores nucleares.
- Un estricto control de calidad con soldadura automatizada y sistemas robóticos ayuda a cumplir con los estrictos estándares de seguridad requeridos.
2. Intercambiadores de calor criogénicos:
- Para aplicaciones en plantas de gas natural licuado (GNL), donde intervienen temperaturas extremadamente bajas, se necesitan técnicas de soldadura especializadas para evitar la fragilidad del material.
- Los posicionadores de soldadura ayudan a garantizar el posicionamiento preciso de las piezas durante el proceso para evitar puntos de tensión que podrían provocar fallas del material a bajas temperaturas.
3. Plataformas marinas y offshore:
- Los equipos de soldadura y posicionamiento son esenciales para la producción de intercambiadores de calor resistentes a la corrosión utilizados en entornos marinos.
- Los rotadores de soldadura facilitan la soldadura sin costuras de grandes intercambiadores que manejan enfriamiento de agua salada, lo que garantiza la integridad estructural en condiciones corrosivas.
4. Aeroespacial:
- Los intercambiadores de calor en la industria aeroespacial requieren una soldadura precisa para materiales livianos y sometidos a altas tensiones, como las aleaciones de titanio. Los manipuladores de soldadura permiten un control preciso de la antorcha, lo que garantiza soldaduras uniformes y sin defectos.
- Los posicionadores y rotadores permiten una soldadura eficiente en configuraciones complejas, cumpliendo con las estrictas tolerancias de las aplicaciones aeroespaciales.