Los recipientes a presión son contenedores cerrados diseñados para contener gases o líquidos a una presión significativamente diferente de la de la atmósfera externa. Son cruciales para aplicaciones industriales como:
- Almacenamiento de gas: contiene gases como cloro, nitrógeno y productos derivados del petróleo.
- Almacenamiento de fluidos: se utiliza para fluidos en industrias como procesamiento químico, refinación petroquímica y alimentos y bebidas.
- Recipientes de reactor: contienen sustancias bajo alta presión y temperatura para reacciones (por ejemplo, reactores en plantas químicas o instalaciones nucleares).
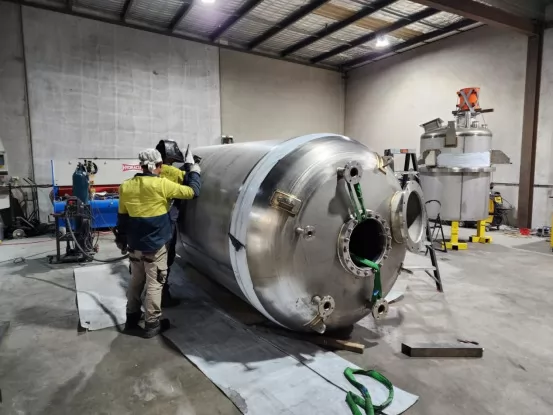
A principios del siglo XX, los recipientes a presión comenzaron a adoptar diseños con refuerzos de acero en espiral y técnicas de soldadura reforzada. Estos avances permiten que los recipientes soporten presiones superiores a 10 000 psi, lo que mejora significativamente su seguridad y durabilidad.
- Soldadura sobre remachado: Inicialmente, los remaches eran comunes en la construcción, pero los recipientes a presión modernos utilizan casi exclusivamente soldadura debido a la resistencia e integridad que proporciona.
- Mejoras de seguridad: Los accidentes históricos resaltaron la importancia de la precisión y la calidad en la fabricación, lo que impulsó estándares estrictos en los procesos de diseño y fabricación.
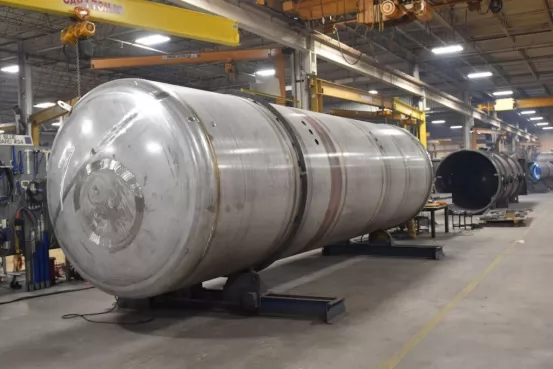
Los recipientes a presión constan de los siguientes componentes:
- Cilindro: El cuerpo principal, normalmente cilíndrico, proporciona la mayor parte del espacio de contención.
- Cabezas y tapas de los extremos: se sueldan a los extremos del cilindro para sellarlo.
- Bridas: Conectan diferentes secciones y permiten el acceso para mantenimiento.
- Soportes: Los soportes verticales u horizontales estabilizan el buque sobre su base.
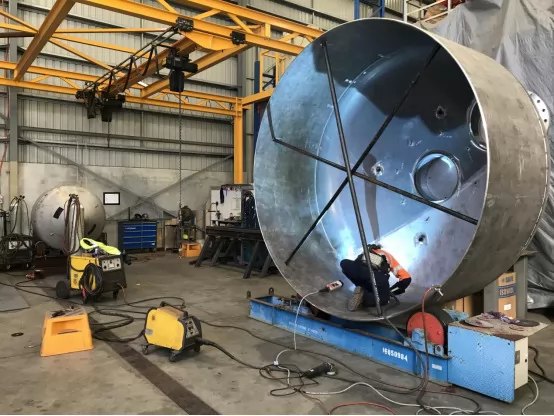
La fabricación implica una secuencia de procesos para garantizar la precisión y la seguridad. Los pasos clave incluyen:
1.
Preparación del material: Las placas de acero se someten a eliminación de óxido, descascarillado y tratamiento de superficie.
2.
Marcado y corte: se dibujan líneas para guiar los cortes y se dan forma a los materiales utilizando métodos de corte mecánicos o térmicos (por ejemplo, corte por plasma).
3.
Conformado y laminado: El cilindro se forma laminando las placas, alineándolas para formar costuras longitudinales.
4.
Soldadura: Una soldadura de alta calidad une cada pieza, especialmente en áreas críticas como las costuras longitudinales y circunferenciales.
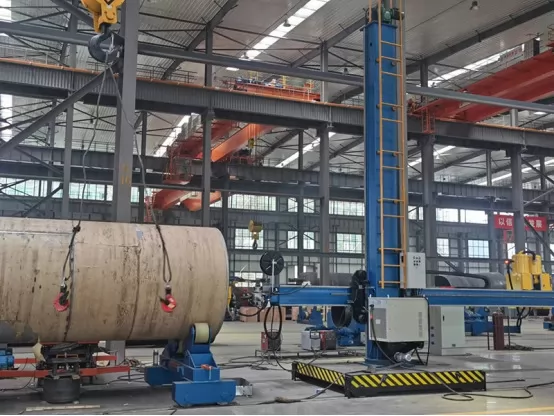
Su equipo de automatización de soldadura y posicionamiento desempeña un papel fundamental para garantizar la precisión, la eficiencia y la seguridad en la fabricación de recipientes a presión. A continuación, le indicamos cómo:
Rotadores de soldadura
Los rotadores de soldadura sostienen y giran las secciones del recipiente cilíndrico, lo que permite:
- Velocidad de soldadura constante: al ajustar la velocidad del rodillo, se optimiza la velocidad de rotación para una soldadura uniforme, lo que garantiza costuras de soldadura ininterrumpidas y de alta calidad.
- Operación manos libres: la embarcación se puede girar mediante control remoto, lo que reduce la fatiga del operador y minimiza los riesgos de manipulación.
- Precisión en el posicionamiento de la soldadura: Los rotadores autoajustables se alinean automáticamente con el tamaño del cilindro, proporcionando soldaduras longitudinales y circunferenciales perfectas.
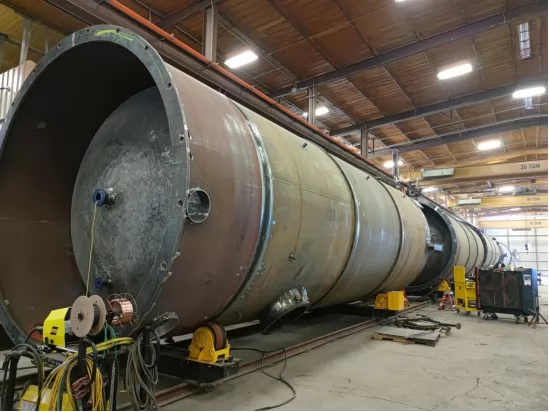
Manipuladores de posicionamiento
Los manipuladores de posicionamiento permiten realizar ajustes precisos de la pieza de trabajo, mejorando el acceso y la calidad de la soldadura.
- Ajustes verticales y horizontales: Estos manipuladores levantan, inclinan o giran los recipientes para proporcionar a los soldadores ángulos óptimos para áreas de difícil acceso.
- Alta capacidad de carga: adecuados para manipular componentes pesados, los manipuladores son esenciales en la fabricación de recipientes grandes, ya que reducen la necesidad de reposicionamiento manual.
- Seguridad mejorada: La automatización reduce el manejo manual de embarcaciones pesadas, minimizando accidentes y garantizando la alineación con los estándares de seguridad regulatorios.
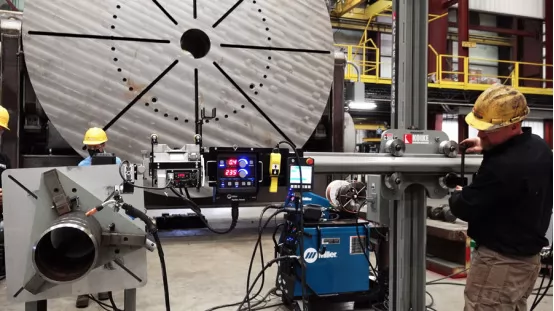
Equipos de soldadura automatizados
La tecnología de soldadura automatizada en la fabricación de recipientes a presión implica:
- Calidad constante: la automatización permite soldaduras precisas y repetibles, lo que garantiza que cada unión cumpla con los estándares de resistencia e integridad.
- Eficiencia: Los sistemas automatizados reducen el tiempo necesario para la configuración y la soldadura, mejorando significativamente las tasas de producción.
- Control multieje: Las máquinas con capacidad multieje permiten realizar operaciones de soldadura complejas, como costuras circunferenciales y longitudinales, sin reorientación.
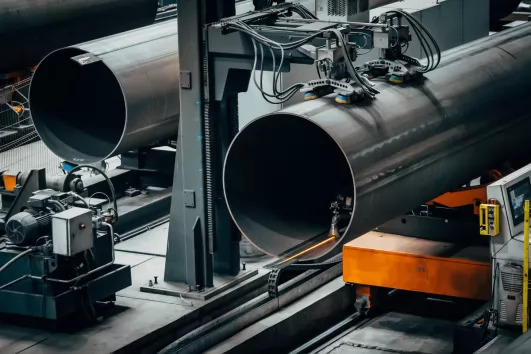
Beneficios integrales del uso de equipos automatizados en la fabricación de recipientes a presión
La implementación de la automatización en la producción de recipientes a presión tiene varias ventajas clave:
- Precisión mejorada: el equipo automatizado minimiza el error humano, garantizando que las dimensiones y las soldaduras del recipiente estén dentro de tolerancias estrictas.
- Mejoras de seguridad: la automatización reduce la necesidad de participación humana en tareas peligrosas, como la manipulación de secciones grandes y pesadas y la soldadura en entornos de alta temperatura.
- Mayor rendimiento: los sistemas automatizados facilitan un procesamiento más rápido, reduciendo el tiempo general de fabricación y manteniendo la calidad.
- Costo-eficiencia: Aunque la inversión inicial es alta, los sistemas automatizados reducen los costos laborales y el desperdicio, mejorando la rentabilidad a largo plazo.
Normas de seguridad y calidad
Debido a la naturaleza peligrosa de los recipientes a presión, el cumplimiento de las normas de seguridad es fundamental:
- Normas ASME: Cumplir con las pautas ASME para el diseño, la selección de materiales y la construcción garantiza que los recipientes resistan la presión y el uso previstos.
- Pruebas no destructivas (NDT): Los métodos de inspección posterior a la soldadura, como pruebas ultrasónicas, radiografías y pruebas con líquidos penetrantes, garantizan la integridad de la soldadura y detectan cualquier defecto.
- Procedimientos y calificaciones de soldadura: Los soldadores y los procedimientos están certificados según los estándares de la industria para garantizar una mano de obra consistente y confiable.
Orientaciones futuras e innovaciones
El futuro de la fabricación de recipientes a presión probablemente verá una mayor integración de la automatización:
- Robótica en soldadura: Los robots manejarán soldaduras cada vez más complejas, mejorando la consistencia y la calidad en aplicaciones de alto riesgo.
- Sensores inteligentes y monitoreo: Los recipientes a presión equipados con sensores inteligentes pueden monitorear continuamente las condiciones y detectar problemas potenciales antes de que se agraven.
- Materiales avanzados: La investigación en materiales como metales compuestos y aleaciones resistentes a la corrosión permitirá que los buques soporten entornos más duros y presiones más altas.
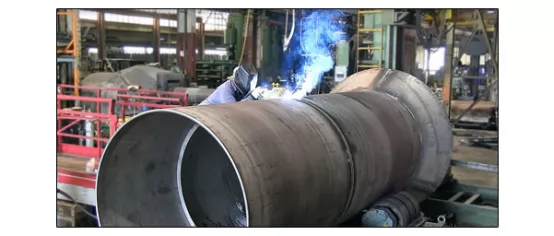